Calm down, you’re just melting plastic, or so we’ve been told. Here’s why we won’t and why there’s much more to it than what’s visible at first glance.
The transformative power of 3D printing extends far beyond mere technological innovation. It represents a fundamental shift in economic thinking about production, inventory, and entrepreneurship. Traditional manufacturing required massive upfront investments, complex supply chains, and significant financial risk. Entrepreneurs had to predict market demand months or even years in advance, committing substantial capital to produce inventory that might never sell.
Paradigm-shift is a strong word, and significantly overused. But with 3D printing, the above mentioned paradigm has been completely inverted. Now, businesses can operate on a just-in-time model where products are created only after a customer places an order. This approach eliminates warehouse storage costs, reduces waste, and dramatically lowers the financial barriers to entry for new businesses. An individual with a laptop and creative design skills can now compete with established manufacturers, testing product concepts with minimal financial exposure.
Rethinking Product Development in the 3D Printing Era
The days of chasing the “one big hit” product are over. Traditional entrepreneurship used to revolve around creating a single, perfect invention that would revolutionize the market. However, 3D printing has dramatically transformed this landscape, offering a more agile and cost-effective approach to product development. In the old days, developing a product entailed lots of upfront cost factors ranging from material cost, cost for potential molds, international shipping and warehousing. But now, 3D printing has created a completely new way of making stuff that makes that old model as outdated as trying to ship out a catalog to get people to your website.
Entrepreneurs used to spend months, even years, meticulously crafting a single product, believing that thorough planning would guarantee success. The reality is a very different one. About 90% of physical product businesses fail. It’s like playing a high-stakes game where the odds are stacked against you, with each iteration costing significant time and money.
It’s Time to say Goodbye to the Old Myth of Product Perfection
The real power of 3D printing lies in its flexibility. Unlike traditional manufacturing, which demands large upfront investments and often very largy minimum order quantities, 3D printing allows for:
- Zero-cost product creation
- On-demand manufacturing
- Instant market testing
- Minimal financial risk
The New Approach: Rapid Iteration and Adaptation
Successful modern entrepreneurs are leveraging 3D printing to:
- Create multiple product variations
- Quickly test market response
- Pivot based on customer feedback
- Continuously improve without significant financial burden
Real-World Success Stories
Consider brands like:
- Ethereal Lighting: Experimenting with unique lamp designs
- Foam Warfare Accessories: Constantly evolving Nerf gun add-ons
- Culinary Creators: Developing innovative cookie cutter collections
- Playful Mechanics: Designing trending fidget toy variations
The Key to Success: Embracing Continuous Innovation
Much like how tech companies A/B test website elements, entrepreneurs can now do the same with physical products. Success no longer depends on creating the perfect item first but on:
- Willingness to experiment
- Quick learning
- Adaptability
- Persistent innovation
Conclusion
3D printing has somewhat democratized product development. It’s no longer about the single, perfect invention but about creating a dynamic, responsive business model that is willing to see some products and ideas fail, to learn from these failures and evolve with market demands.
The economic implications are profound. Small creators and entrepreneurs can now experiment with niche markets, creating highly specialized products that would have been economically unfeasible under traditional manufacturing models. A designer in a small town can now create and sell custom products globally, reaching customers who were previously unreachable due to high production costs.
Moreover, this model encourages a more sustainable approach to manufacturing. By producing only what is immediately needed, 3D printing reduces industrial waste, minimizes excess inventory, and allows for more personalized, on-demand production. It transforms manufacturing from a mass-production model to a flexible, responsive ecosystem that can quickly adapt to changing consumer preferences and emerging market trends.
We are now at a point where we can produce hundreds of items per week, reliably and locally. If you have a product idea or are in the market for small scale precision manufacturing from PLA to high-strength engineering materials, contact us and experience a new form of competitive manufacturing.
Thanks for reading and have a nice day!
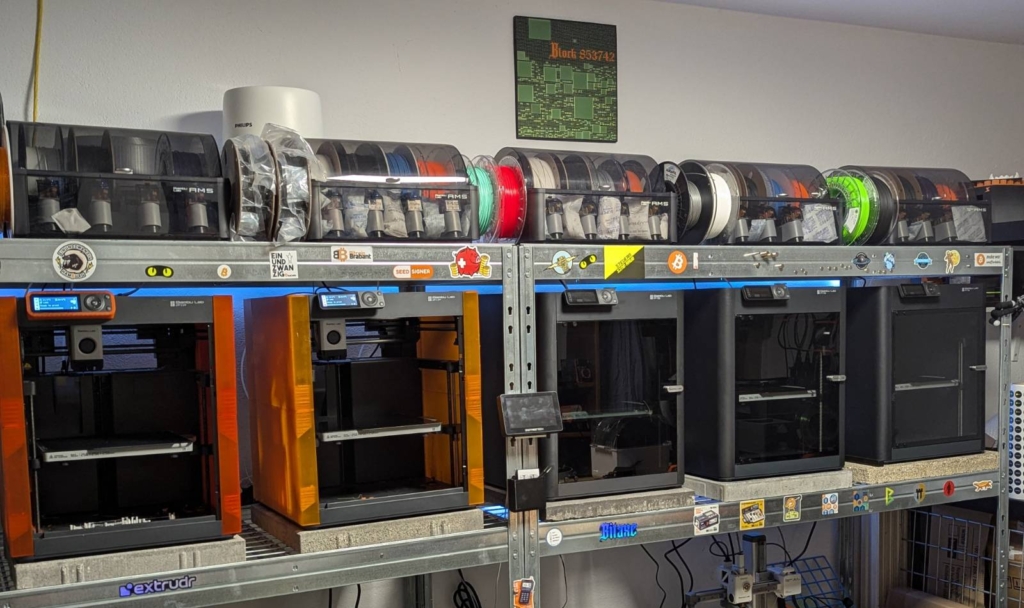